Every year many of us in the industry share our stories of “Peak Season” that are almost always what now seems to be a relatively innocuous set of challenges revolving around ramping up staff, adding more temporary workstations or bringing in some rental equipment and devices while being extra vigilant to monitor shipping volumes and timing.
In fact, many of us built our careers sharing expertise on how to handle Peak Season and all the possibilities it presents us – the good, the bad and the ugly.
While we all generally felt our way through the dark of the pandemic in 2020 without a good road map and perhaps without as much post-peak reflection perhaps because it seemed like an anomaly we hoped to never repeat.
But oh, we were so wrong!
We’ve been hearing about (and for many of us, experiencing) all the disruptions, shortages, and general unpredictability of global, regional and local supply chains. But the way all of these things are coming together now as Peak Season ramps us reads almost like a sci-fi disaster movie, or a comedy albeit a tragic one)!
How CrAZy Is It? Let Us Count The Ways…
We’re not going to pretend to have the simple, high-level view of what is going on here. Others who make careers doing that will tell us more after the season is over. But here is just a sampling of some of the disruptions and distortions that you may or may not be aware of:
1. Plastics – from our own experience, we’ve had to scramble to keep up with the surge in demand this year in part because of the cost increase and limited supply of the chemicals used to make the plastic pellets we all rely on for manufacturing plastic parts. Hurricane Laura in 2020 instantly reduced by 15% the production of polyethylene (PE) and polypropylene (PP), and the deep freeze in Texas in February set them back another 12% or so. Add in the Suez Canal block, spikes in shipping costs from Asia, Brexit (adding paperwork), labor shortages AND higher demand. Depending on which plastic you are looking for, prices are now 5-10x higher per pound than a year ago.
CAN IT GET WORSE? Hurricane Season is here – with Hurricane Ida leaving about 60% of production offline during the middle of September. Hang on!
2. Containers – The humble, yet mighty container shipping industry is now starting to look like a luxury brand. While a 40 foot container rented to ship your stuff from Asia used to run about $1,400 to $2,000, businesses are now reporting spending anywhere from $14,000 - $20,000 for a single unit! How bad is it?
- Costco is now renting its own container ships to reduce the impact on their supply chain? Yes, Cosco has reportedly locked in use of 3 entire container ships to help lessen the severity of delays on their supplies.
- America’s ports in Los Angeles and Long Beach (accounting for 47% of imports) set seven new records in just four weeks for wait times, with 65 ships waiting in line to be offloaded two weeks ago, which translates into an average wait of OVER EIGHT DAYS increasing the door-to-door time to over 71 days!
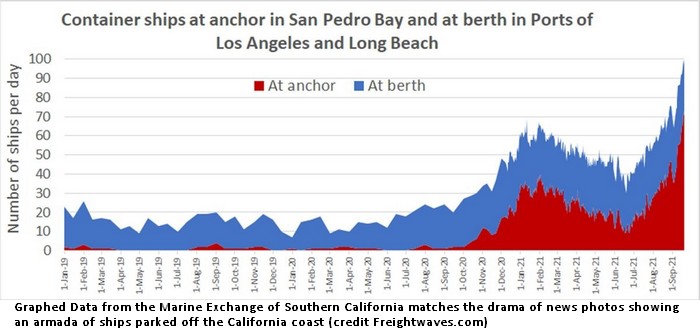
- For every 100 containers that arrive in the US, ONLY FORTY ARE GOING BACK? That’s right, 60% of all the containers arriving here are sitting here, empty, creating gigantic shortages in Asia and Europe (driving up the price even more).
CAN IT GET WORSE? Well, through 2020 and into Q1 of this year, the scrapping of old containers (generally after 15 yrs) was still exceeding production of new ones.
3. Transport and Storage Costs – We won’t spend a lot of time on transportation, we’re all familiar with the challenges – shortages of drivers driving shortages of capacity in particular. But one side effect of that problem is a massive increase in the cost of warehouse space. Why? Manufacturers and Distributors have learned that part of the solution to their transportation problem comes from shortening the distances required to their destinations. The result is a massive acceleration of distributed storage for those who can afford it – because prices for leased space are higher than ever. How has it played out? A recent article from GlobeSt.com has some eye-popping numbers:
- Leased industrial space is at an all-time high reaching almost 600 million feet, a rise of more than 50% over 2020.
- 3PLs now account for about 1/3 of all bulk industrial space (>100,000 sf), doubling their leased space from 2020!
- Warehouse vacancy rates have dropped to less than 4 percent, with the first-year lease rate rising almost 10%.
CAN IT GET WORSE? We skipped transportation for this section, but can’t leave without mentioning that drayage rates increased a whopping 32% in September (per BookYourCargo) and that warehouse storage space shortages are expected to last at least into 2023.
How Do We Manage A Peak Like No Other?
As we write this, it’s become apparent that this week’s article feels a bit more like a pre-Halloween horror story, especially if your business is impacted by most, if not all of those individual anecdotes and data points mentioned above. As we stated at the top of this article today, we are not going to try to predict how or when these issues all resolve themselves. Like many of you, we are here to try to help many of our customers in these industries and others impacted by them while also managing through the same challenges for our own manufacturing and distribution.
While the “Can It Get Worse?” refrain was done tongue-in-cheek, it does recognize that we are still in uncharted territory and that we can’t really make assumptions about the next 3, 6, or 12 months. However, making the adjustments we can make, planning farther ahead, resetting expectations – along with a little bit of hope for some of the external factors to work themselves out (sometimes in spite of ourselves!) will be the key to surviving – or even thriving – between now and 2023.