Receiving in a manufacturing environment is an overlooked process area that can be the start of numerous bottlenecks, accuracy errors and wasted motion. A few simple tools that have transformed receiving in the logistics world can be leveraged in a manufacturing environment to radically change the outcomes and improve your metrics in this critical process area while achieving a positive ROI in less than 12 months.
Most Receiving Docks Have THIS Specific Problem in Common
Look at 100 different manufacturing facilities on a value stream or process level, and it is possible to imagine that you might find 100 different processes that don’t look too much alike for any given value stream. Every industry, and sometimes every product has its own unique needs that drive a lot of customization, from tooling to packaging, environmental controls and more.
However, Receiving - where parts, materials or products are received into your facility onto a dock from trucks (or trains) - is one major process area that both looks and functions almost exactly the same way in most facilities everywhere. The typical Receiving process is fairly simple, and will look something like this:
- Truck backs up to open bay on Receiving dock.
- Pallets are removed and placed on Receiving dock.
- Staff affixes labels to pallet or boxes on pallet with barcoded information indicating information like status (i.e. “received”, product info, storage location, etc.).
- Life driver moves pallet to designated storage location (or production line)
- Pallet (or boxes) are scanned in at storage location or destination production line.
As simple as it sounds, this process is full of wasted movement because most facilities print up labels for the incoming shipments in a central location, and then they are retrieved and carried to the Receiving dock by the staff for each pallet from the printer – usually located in an office in the facility. In some operations, labels are printed in sets for each pallet, and it often results in workers making multiple trips to the printer in order.
What the typical Receiving process results in is a LOT of footsteps. The repeated trips to a stationary printer, regardless of where it is, mean that staff need to walk to retrieve labels. Even if the printer is out on the Receiving dock, a facility with 10 bay doors that average 14’ per bay (door and adjacent wall space), will be 140’ long, meaning a printer placed right in then center would still mean trucks arriving at the bays on the end will generate 140’ of walking per trip for a worker retrieving labels for that delivery – or about 50 steps. Multiply that by potentially dozens of different arrivals every day and your Receiving team will be taking thousands of steps every day that represent a significant waste of both labor cost and fatigue.
AND…in addition to the major problem of wasted steps, our customers have reported other problems including:
- Inventory Accuracy - Misplaced pallets result in inaccurate inventory and can occur when a lift driver takes away to storage a pallet that has not been processed yet, often when the Receiving dock staff is away retrieving labels.
- High Detention Fees – for facilities with high velocity, the slower processing in Receiving creates delays for trucks waiting to offload. Fees run from $25-$90/hour after a two-hour grace period. A faster Receiving process avoids this.
- Production Delays – for lean operations using “just-in-time” or similar approaches to supplying parts, bottlenecks at the Receiving dock can result in costly shutdowns of production lines while waiting for Receiving to process incoming parts or raw materials.
Optimizing Receiving in Three Steps
If you are like most facility managers, optimizing Receiving was probably not as high on your task list as it might be now after reading this. There is a lot of science, process analytics, engineering and design work done around nearly every other process in your facility and Receiving is often overlooked. It is perhaps because of its uniformity across all businesses that many don’t consider it as a priority for re-engineering, but many facilities now know better and have implemented some excellent solutions with measurable results.
Here is how we recommend making receiving work better for your facility too:
Step 1 – Document and analyze your existing process.
While most businesses have done extensive work and planning on developing some of their core processes like picking and packing, we’ve found over the years that many of the Receiving processes out there were just developed organically without a lot of intent or regard for productivity. This is in part due to the deceptively simple appearance of what’s involved in Receiving.
So as a first step, document what happens every day on your Receiving dock. Include every step from when the truck arrives (or even when its arrival time is communicated) all the way through to when the pallets and boxes are moved off of the dock after processing and sent to a production line or storage. Look to collect data regarding how much time it takes to process a pallet, or unload a truck, how many people-hours required for a shift, how many steps does everyone take during the process, the location of key equipment, distance from dock to rack or line, etc.
If you are a small-medium business, you most likely don’t have an internal process engineer, but that doesn’t mean you can’t measure and analyze. For listing up and measuring each part of the process, use an app like “Motion Meter”, which allows anyone to document their own process quickly.
Step 2 – Deploy a mobile workstation solution with on-demand printing.
While carts with independent power supplies are now growing in popularity in a large variety of process situations and industries, there is no process area where a mobile workstation has a more immediate impact than in Receiving. Nearly every user gets their first mobile workstation in the Receiving area because it is the easiest place to implement it and immediately makes a visible difference in productivity.
The biggest difference from Day 1 will be to see how much more quickly each truck or pallet gets processed. This is because your label printer is now on wheels and labels can be printed on demand as they are needed while the printer easily moves from pallet to pallet where it is needed. The operator can circle around the pallet, scanning and labeling as they go, and when done can signal your lift driver to remove the pallet to its next destination. Productivity increases of up to 50% are not uncommon.
To see a comparison of how a typical Receiving process compares to one with a mobile printer, watch the short video below of a side-by-side comparison:
Step 3 – Go beyond simple barcodes to bring more speed.
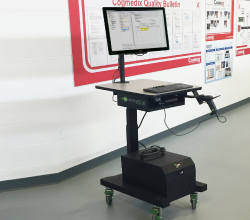
Another user in changed the storage of their valuable archived items by affixing RFID tags to each item and its container. Taking inventory now only takes minutes by using a cart with a lithium battery pack to power three RFID antennae mounted on a telescoping pole.
Finally, think about updating your printer too. New color printers have become much more productive and cost-effective, meaning that color can be incorporated into your label printing which opens up a lot of interesting possibilities, including:
- Eliminating the need for pre-printed labels (and the cost of ordering large quantities and storing them).
- Creating visual cues on labels that could eliminate the need for some scans and barcodes (i.e. color code a destination rack a lift-driver can see and act on.
- Improve identification techniques – one manufacturer is now dynamically printing labels on parts boxes that show a picture of the part inside.
Big Changes Don’t Always Need Big Investments
If you are like most manufacturers, you will always start to see opportunities for improvement simply by starting the process of documenting and analyzing your existing processes. Inevitably there will be areas of waste identified – motion, materials, time or space – and some changes will seem obvious even before you look at solutions like a mobile workstation.
But when you decide to redesign your process, do so with the awareness of what types of equipment can make a big difference. Being aware of the availability of new tools and solutions will help shape the thinking on how the new version of the process will look.